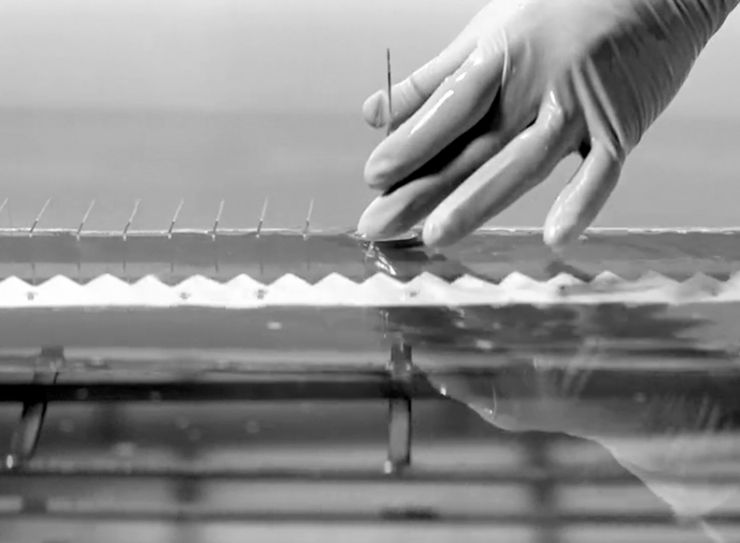
Glass Cleaning
At Coresix, cleanliness is treated as an independent technology; procedures for which are continuously monitored and improved upon. With many of today’s technologies, the introduction of foreign matter to the process can have a serious impact on production yields and product performance. Coresix provides a unique niche in our ability to clean glass and maintain the highest level of cleanliness to the customer’s door.
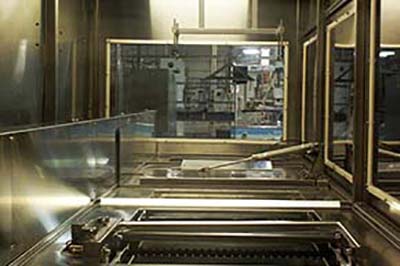
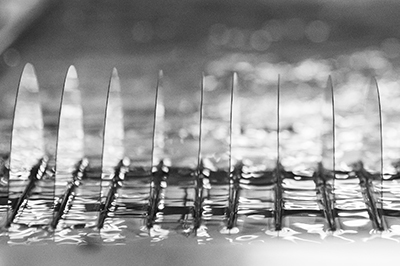
Glass Cleaning Process
All steps in the fabrication process prior to cleaning can have an impact on the cleanliness of the final product. Therefore, our entire process is engineered to minimize the introduction of particulate and to maximize the effectiveness of our cleaning procedures.
The standard cleaning procedure for most glass components produced at Coresix is a Mechanical Scrub followed by an Ultrasonic Wash which feeds directly into a class 100 Optical Clean Room. We combine ultrasonics and megasonics on multiple cleaning lines which feed directly into a Class 100 Clean Room.
Particulate: Any debris which is external to the glass component. For our purposes, we consider non-removable particulate as debris that can not be removed with an air gun.
Spots and Stains: Any non-particulate residue or pattern left on the surface of the glass after final preparation such as water spots, haze, streaks, etc.
Coresix has various inspection methods and standards for cleanliness and packaging depending on the sensitivity of the application to particulate and stains.
Mechanical Wash
As a standard, glass components are scrubbed to remove heavy particulate such as glass residue from grinding operations, polishing compounds, and other elements typically not affected by ultrasonics.
Ultrasonic Wash 1
Unless otherwise specified, all glass components less than 300mm diagonal are cleaned through our 10-stage Ultrasonic Line. The first and third stages use an optical soap, and the second and fourth through ninth are progressively filtered DI water rinses. The final stage is an IPA vapor bath which removes residual moisture from the parts.
Ultrasonic Wash 2
Coresix runs a second Ultrasonic Wash line with size capabilities up to 550mm in diameter. This is a 6 stage system with a slow pull, filtered air dry. This line runs in tandem with the USW1 and also feeds directly into the Class 100 Clean Room.
Clean Room
Our optical clean room is a completely darkened environment for maximum effectiveness of the inspection lighting and is certified as Class 100. All cleanliness and surface quality critical components are inspected and packaged within the clean room.
Class 100 Optical Clean Room
Cleanrooms are classified according to the number and size of particles permitted per volume of air. Large numbers like "class 100" or "class 1000" refer to FED-STD-209E, and denote the number of particles of size 0.5 µm or larger permitted per cubic foot of air.
A class 100 cleanroom maintains less than one hundred particles larger than 0.5 microns in each cubic foot of air space.